Woodworking has shaped human civilization for thousands of years. From simple tools to intricate furniture, this craft has been vital to our progress.
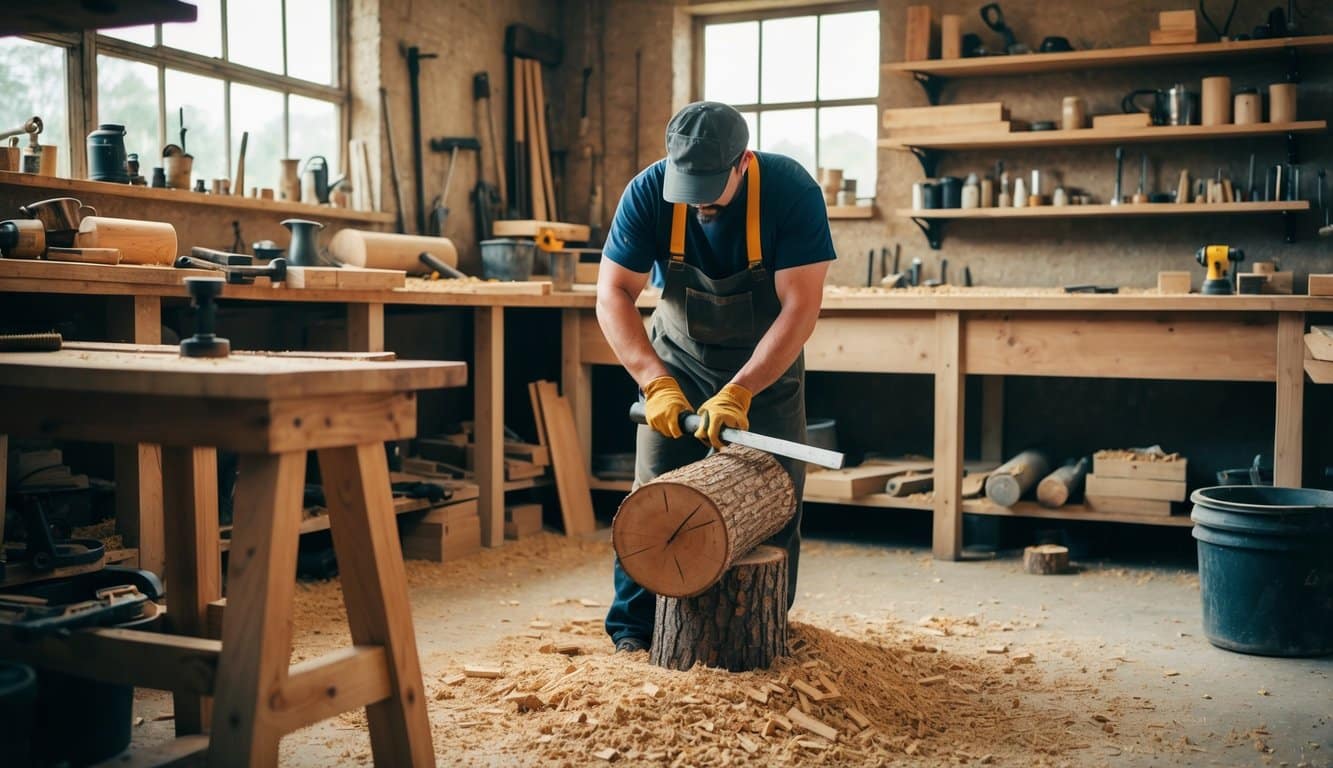
You can trace woodworking back to prehistoric times when early humans first used wood to make weapons and shelters. As societies grew, so did woodworking techniques.
Ancient Egyptians created wooden furniture and boats, while Chinese artisans built temples and palaces.
The Middle Ages saw woodworking become a respected trade. Guilds formed to protect the craft’s secrets and train new generations.
Today, woodworking remains popular as both a hobby and a profession. Modern tools have made it easier, but the basic skills are still rooted in ancient practices.
Early Woodworking Origins and Techniques
Woodworking has ancient roots dating back thousands of years. Early humans used wood to create tools, shelter, and other essential items.
As civilizations grew, woodworking techniques became more advanced.
Prehistoric Times to Ancient Civilizations
You might be surprised to learn that woodworking began in prehistoric times. Early humans used stone tools to shape wood. They made spears, clubs, and handles for stone axes.
As time passed, they created more complex items like bowls and containers.
Primitive tools like axes and adzes were crucial for working with wood. These tools allowed people to cut down trees and shape logs.
Bow drills were another important invention. They helped create holes in wood for joining pieces together.
Woodworking in Ancient Egypt
Ancient Egyptians took woodworking to new heights. They used wood to build boats, furniture, and even coffins. Their woodworking skills were quite advanced for their time.
Egyptian woodworkers had a variety of tools at their disposal. These included:
- Copper chisels
- Bronze saws
- Wooden mallets
- Measuring cords
They created intricate designs and joined wood pieces using complex techniques. Egyptians also developed new types of joints to make stronger furniture.
Developments in Mesopotamia and Ancient China
Mesopotamian cultures also made big strides in woodworking. They created elaborate wooden doors and furniture for palaces and temples. Their woodworkers used similar tools to the Egyptians but developed their own unique styles.
In Ancient China, woodworking was highly respected. A legendary figure named Lu Ban is said to have invented many carpentry tools.
Chinese woodworkers created beautiful furniture, buildings, and even machines.
They developed techniques like:
- Mortise and tenon joints
- Lacquering
- Wood bending
These methods allowed them to create sturdy and decorative wooden items that have stood the test of time.
Tools and Technology Evolution
Woodworking tools and techniques have changed dramatically over time. New inventions and materials have shaped how craftsmen work with wood.
The Bronze Age to the Middle Ages
In the Bronze Age, metalworkers created stronger, more durable tools. You could now use bronze chisels and saws to shape wood more precisely.
The Middle Ages brought iron tools that were even tougher. Carpenters used axes, adzes, and drawknives to rough out timber frames.
Planes helped smooth wooden surfaces. Hand drills and augers let you bore holes easily.
The pole lathe appeared, allowing craftsmen to turn wood for chair legs and other round parts.
Renaissance Advances in Woodworking
During the Renaissance, joinery methods became more refined. You could create intricate furniture designs with new techniques.
Dovetail joints added strength to drawers and boxes. Mortise and tenon joints improved chair and table construction.
Better saws emerged, like frame saws and pit saws for cutting planks. Spring poles enhanced lathe turning.
Specialized planes let you create moldings and decorative edges.
Industrial Revolution Impact
The Industrial Revolution transformed woodworking. Steam power drove large sawmills and woodworking machinery.
You could now use circular saws and band saws to cut wood faster and more accurately.
Mass production techniques changed furniture making. Standardized parts and assembly line methods sped up manufacturing.
Power tools like electric drills and sanders made woodworking easier for professionals and hobbyists alike.
Modern Woodworking Tools and Machinery
Today, you have access to a wide range of advanced tools.
Computer Numerical Control (CNC) machines can carve intricate designs automatically. Laser cutters offer precision for thin materials.
Computer-Aided Design (CAD) software helps you plan projects in detail before cutting wood. 3D printers can create custom jigs and parts for your workshop.
High-tech power tools offer improved safety features and efficiency. Dust collection systems keep your workspace clean and protect your lungs.
Craftsmanship and Joinery
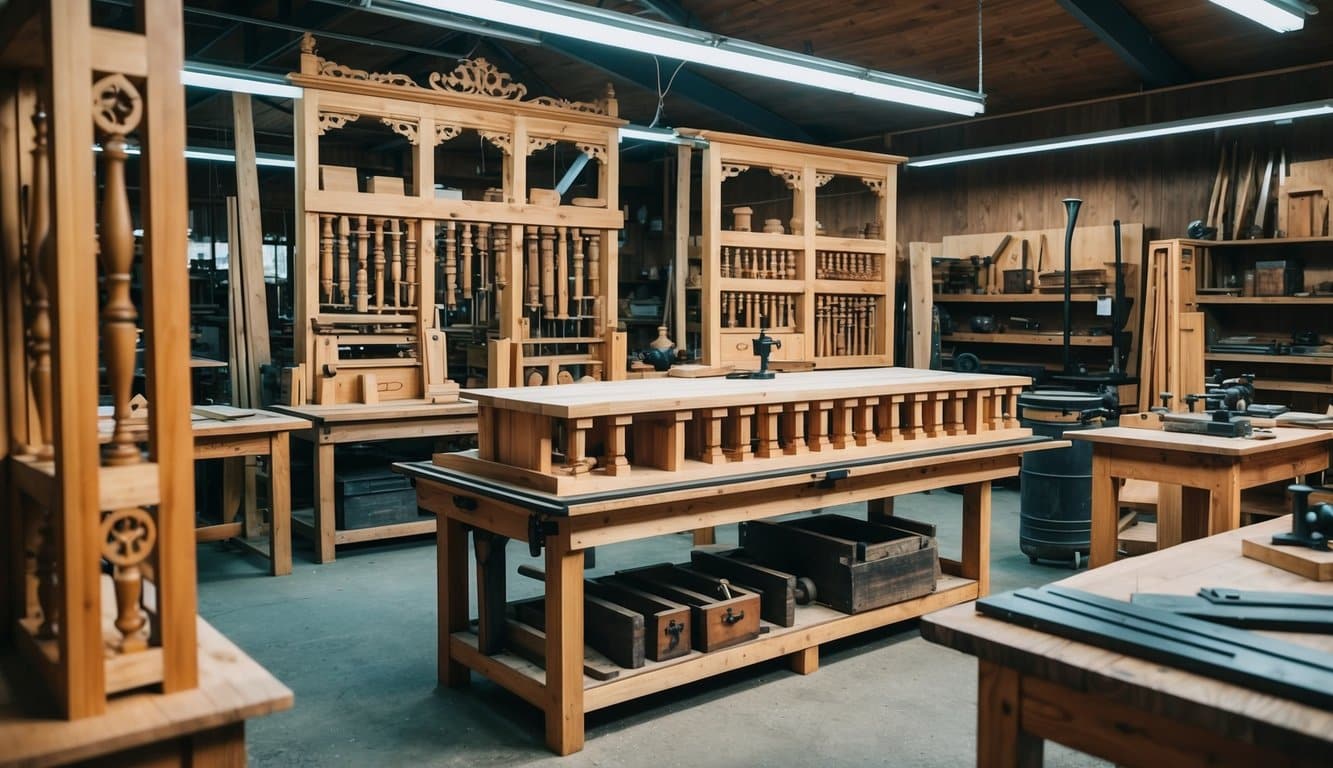
Woodworking has a rich history of skilled craftsmanship and intricate joinery. These techniques have been refined over centuries, allowing artisans to create beautiful and durable pieces.
Traditional Hand Tools and Techniques
You’ll find that traditional woodworking relies on a set of essential hand tools. Chisels, planes, and saws are key to shaping wood with precision.
Hand tools give you greater control over your work.
Skilled woodworkers use these tools to create smooth surfaces and tight-fitting joints.
Planes help you flatten boards and create even surfaces. Chisels let you carve out detailed designs and clean up joinery.
Learning to use these tools takes practice. But once mastered, they allow you to work wood in ways machines can’t match.
Joinery: From Mortise and Tenon to Complex Joints
Joinery is the art of connecting wood pieces. The mortise and tenon joint is one of the oldest and strongest.
You create a hole (mortise) in one piece and a matching projection (tenon) on another.
Dovetail joints are prized for their strength and beauty. They use interlocking “tails” and “pins” to join boards at right angles.
Other common joints include:
- Finger joints
- Lap joints
- Miter joints
Each type of joint has its own strengths and uses in woodworking projects.
Veneering and Marquetry
Veneering involves applying thin sheets of wood to a surface. This technique lets you create beautiful patterns and use rare woods economically.
Marquetry takes veneering further. You cut pieces of veneer into shapes and arrange them to form pictures or designs.
This art form dates back centuries and is still used in high-end furniture.
Both techniques require patience and skill. You must carefully select and prepare your wood.
Precise cutting and fitting are crucial for a seamless final product.
Cultural Significance in Woodworking
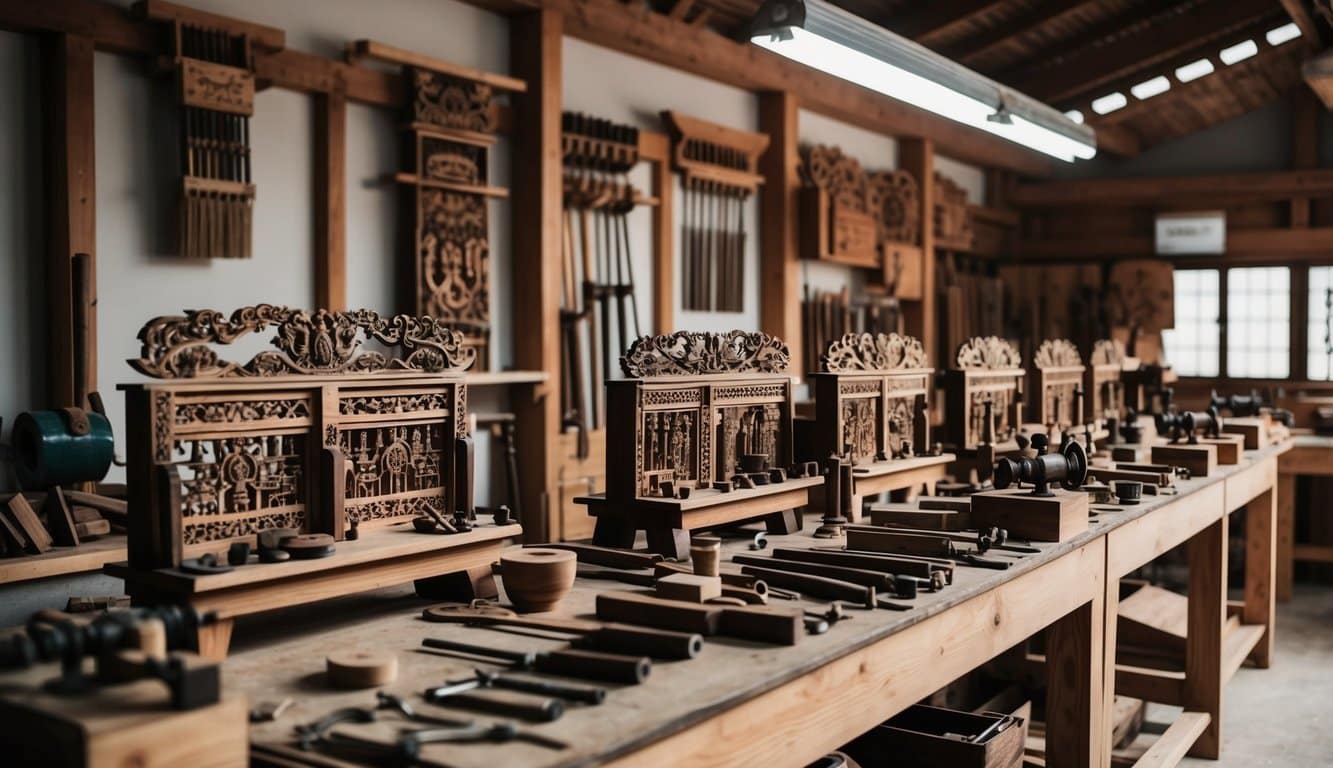
Woodworking has deep cultural roots worldwide. Different societies have developed unique techniques and styles that reflect their values and traditions. These practices have shaped woodworking as both an art form and a practical craft.
Chinese and Japanese Woodworking Traditions
Chinese woodworking dates back thousands of years. You’ll find intricate joinery in ancient temples and furniture.
Chinese craftsmen use tools like the lu ban ruler for precise measurements. They often work with woods like bamboo and rosewood.
Japanese woodworkers are known for their joinery skills. They create complex wooden structures without nails or screws.
You might recognize techniques like:
- Mortise and tenon joints
- Dovetail joints
- Finger joints
These methods result in strong, beautiful pieces that can last for centuries. Japanese carpenters also value the natural beauty of wood grain.
Woodworking Cultures Around the World
Many cultures have unique woodworking traditions. In Scandinavia, you’ll see clean lines and simple designs in furniture.
African woodcarvers create masks and statues with deep cultural meanings.
Native American tribes use woodworking for both practical and spiritual purposes.
You might find:
- Totem poles
- Canoes
- Sacred items
In the Middle East, intricate wooden screens called mashrabiya are common. These serve both decorative and functional roles in architecture.
Vitruvius and the Western Canon of Carpentry
Vitruvius was a Roman architect and engineer. His work shaped Western carpentry for centuries. You’ll find his ideas in many European woodworking traditions.
Vitruvius wrote about the importance of:
- Durability
- Utility
- Beauty
These principles still guide many woodworkers today.
You can see Vitruvian influence in:
- Classical furniture designs
- Architectural woodwork
- Modern carpentry techniques
Western carpenters often use a mix of hand tools and power tools. They work with a wide range of woods, from pine to exotic hardwoods.
Notable Woodworking Practices and Projects
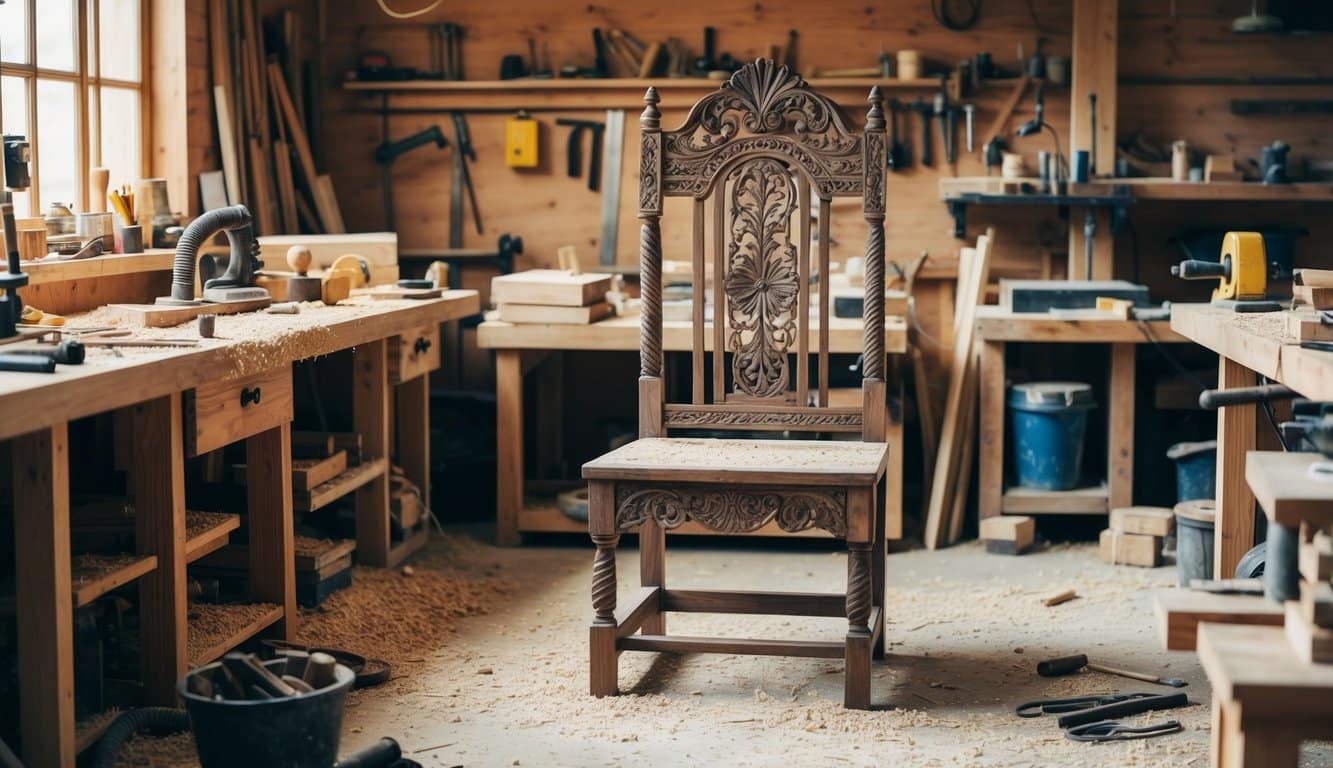
Woodworking has produced remarkable creations throughout history. Skilled artisans have crafted furniture, sculptures, and art pieces that showcase the beauty and versatility of wood.
Historic Furniture Making
You can find stunning examples of historic furniture in museums and stately homes.
Craftsmen used techniques like dovetail joints and marquetry to create durable, ornate pieces.
The 18th century saw the rise of Chippendale furniture, known for its elegant carvings and cabriole legs.
Queen Anne style chairs featured curved backs and shell motifs. Georgian period furniture embraced symmetry and proportion.
These historic styles still influence modern furniture design today.
Cabinetmakers developed specialized tools like planes and chisels to shape wood precisely.
Wood Carving and Artistic Contributions
Wood carving has produced breathtaking art for centuries. You can see intricate religious carvings in churches and temples worldwide.
Master carvers brought wood to life, creating lifelike figures and elaborate decorative elements.
Famous wood sculptures include Grinling Gibbons’ delicate fruit and flower carvings. Native American totem poles tell stories through carved animal figures.
Japanese netsuke are tiny carved toggles used on kimono sashes.
Chip carving creates geometric patterns using small knives. Relief carving produces images that seem to rise from a flat wooden surface.
Whittling is a simple form of carving using just a pocket knife.
Contemporary Woodworking and Art
Modern woodworkers blend traditional skills with new technologies. You can find wooden sculptures that push the boundaries of the material.
Some artists use chainsaws to quickly rough out large forms. Others employ lasers for precise cutting and engraving.
Furniture makers experiment with unconventional designs and mixed materials. You might see a wooden table with resin-filled cracks or metal inlays.
3D printing allows for complex wooden structures that were once impossible to create.
Studio furniture blurs the line between functional objects and art. These unique pieces often showcase unusual wood grains or organic forms.
Eco-conscious artisans use reclaimed wood to create sustainable art and furniture.
Impact of Woodworking on Environment and Society
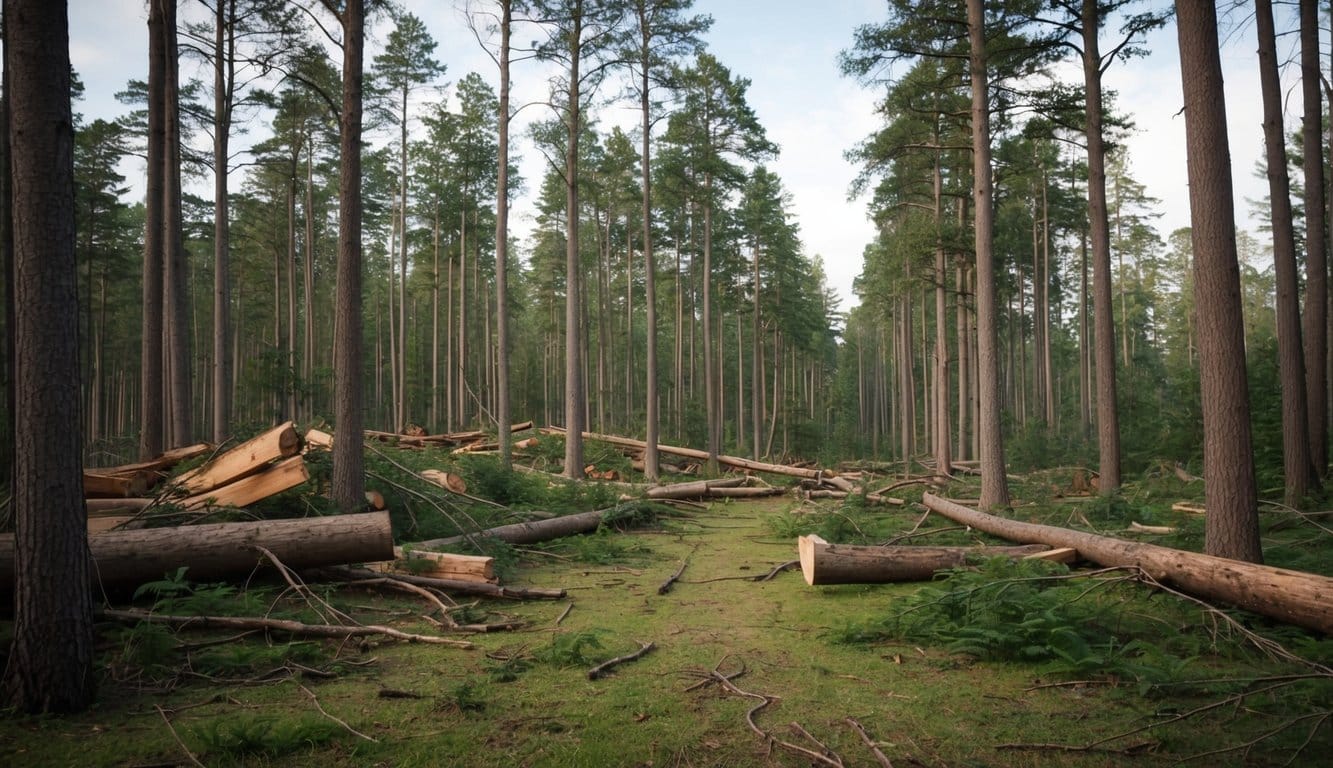
Woodworking has shaped forests and communities for centuries. It has both positive and negative effects on nature and people’s lives.
Deforestation and Timber Use
Timber harvesting for woodworking has led to widespread deforestation. You can see this impact in many parts of the world.
Forests shrink as trees are cut down for lumber and plywood. This harms wildlife habitats and reduces biodiversity.
The demand for rare woods puts some tree species at risk. Mahogany and rosewood face threats from over-harvesting.
Illegal logging also damages forests in many countries.
But not all news is bad. Some wood products, like plywood, use trees more efficiently. This helps reduce waste.
Many furniture makers now use fast-growing woods to ease pressure on old-growth forests.
Sustainable Practices in Modern Woodworking
Green woodworking methods are growing more common. You’ll find many shops using eco-friendly techniques today.
These aim to protect forests and cut down on waste.
Certified wood from well-managed forests is now widely available. Look for labels like FSC when you buy wooden items.
This ensures the wood comes from responsibly grown trees.
Reclaimed wood is another eco-smart choice. Old barns and buildings provide timber for new projects.
This gives wood a second life and reduces the need to cut fresh trees.
Some woodworkers use only local woods. This cuts down on transport emissions. It also supports nearby forest management efforts.
Educational Pathways and Professional Development
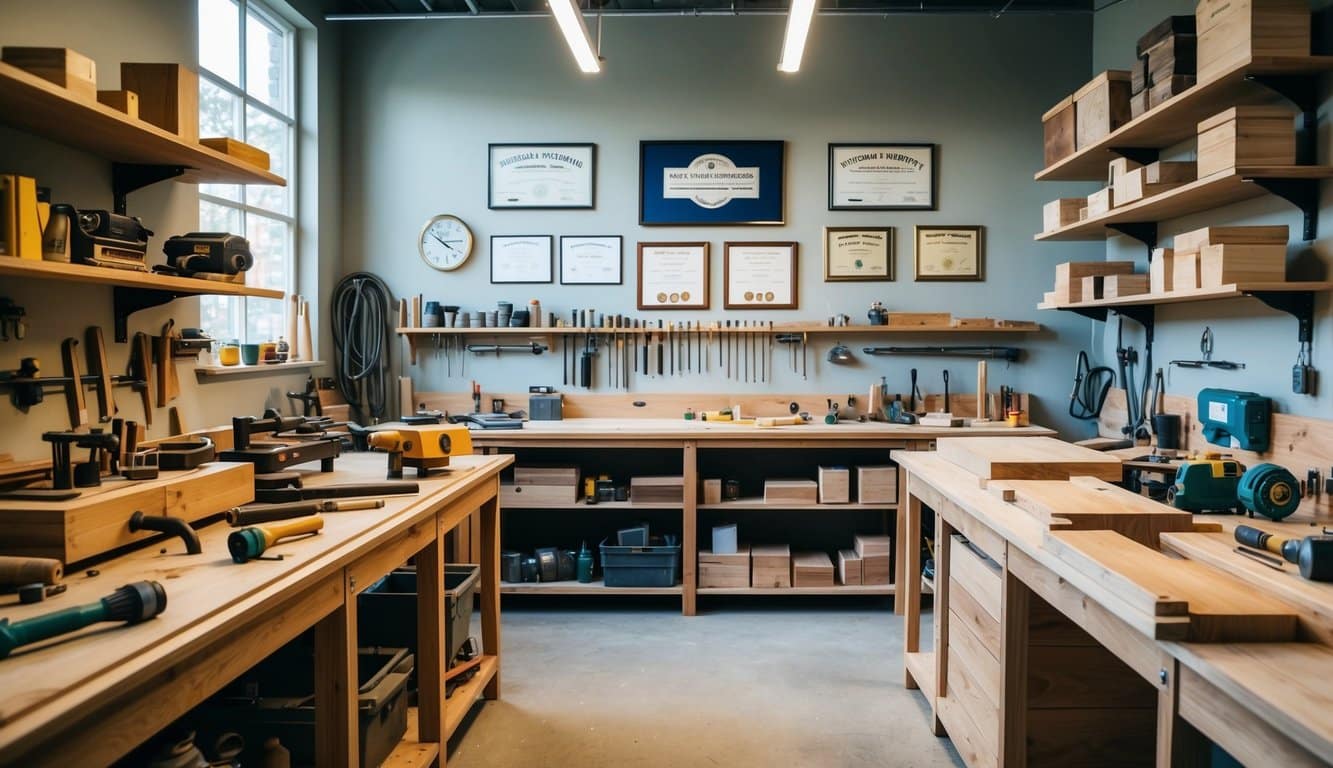
Woodworkers have several options for learning their craft and advancing their careers. These paths combine hands-on training with formal education to develop skills and expertise.
Apprenticeship and Learning the Craft
You can start your woodworking journey through an apprenticeship program. These programs pair you with experienced craftspeople to learn on the job.
You’ll gain practical skills in using tools, reading blueprints, and working with different types of wood.
Many vocational schools and community colleges offer woodworking courses. These classes teach you the basics of design, joinery, and finishing techniques.
You’ll also learn about wood properties and how to select the right materials for projects.
Online tutorials and workshops are another way to build your skills. These resources cover everything from basic techniques to advanced furniture making.
They let you learn at your own pace and try new methods in your home workshop.
Guilds and Professional Organizations
Joining a woodworking guild can help you network and improve your skills. Guilds often host workshops, lectures, and exhibitions.
You’ll meet other woodworkers and learn about new techniques and tools.
Professional organizations like the Woodworkers Guild of America offer resources for both hobbyists and professionals.
They provide access to expert advice, project plans, and discounts on tools and materials.
These groups also offer certification programs. Getting certified can show your expertise and help you attract clients.
It may lead to better job opportunities or higher pay in your woodworking career.
Materials and Finishing Techniques
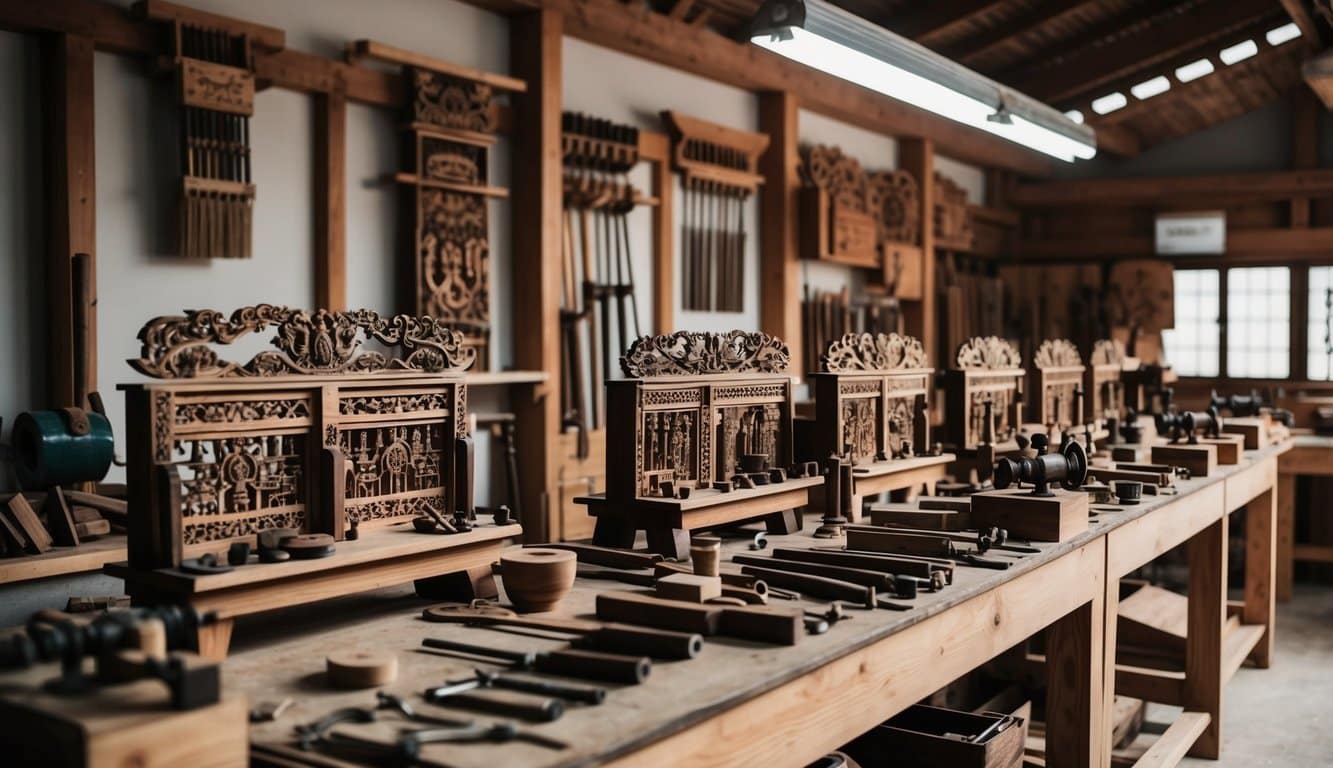
Woodworkers use a variety of materials and techniques to create beautiful pieces. The right wood and finish can make all the difference in the final product.
Choosing the Right Wood
When picking wood for your project, consider hardness, grain pattern, and color.
Oak is strong and durable, perfect for furniture. Pine is softer and easier to work with, great for beginners.
Cedar resists rot, making it ideal for outdoor projects.
Think about the wood’s moisture content. Dry wood is less likely to warp or crack.
You can buy kiln-dried lumber or air-dry it yourself.
Don’t forget about engineered woods like plywood or MDF. These are stable and cost-effective options for many projects.
Use of Varnishes and Protective Finishes
Finishes protect wood and enhance its beauty.
Oil-based varnishes are durable and bring out the wood’s natural grain. They take longer to dry but offer great protection.
Water-based finishes dry quickly and have less odor.
They’re easier to clean up but may not be as tough as oil-based options.
For a natural look, try Danish oil or tung oil.
These penetrate the wood and offer some protection without a thick coating.
Polyurethane is very durable and comes in different sheens.
It’s great for high-wear surfaces like tabletops.
Remember to sand between coats for a smooth finish.
Always work in a well-ventilated area when applying finishes.